Efficient home design and lessons from the Foursquare Farmhouse
Three years after the 2008 housing crash, builders started building homes again—but with fewer workers. Ten years later, the residential building industry still hadn’t fully regained its pre-2008 labor force. During this period, material costs slowly increased—and then dramatically climbed during the pandemic. The decreased labor force combined with increased material costs have dramatically increased overall new home construction costs—a reality which has fostered a renewed interest in finding ways to reduce them.
The custom home-building process is focused on first meeting a homeowner’s goals and constraints, before seeking design efficiency—leading homeowners to manage their budgets based on the home’s overall size and perceived per-square foot costs. This is a fine place to start, but the best way to reduce cost—whether constructing a house or manufacturing a car—is finding efficiency in both design and construction.
Sears & Roebuck understood this back in 1908 when it started offering mail-ordered homes. After a few years selling homes, Sears realized it needed to get more efficient at constructing and shipping homes in order to increase sales. This led Sears’ team to develop pre-cut lumber (now studs), plasterboard (now drywall), and asphalt shingles, to name a few—all products still used today, some 100 years later.
Further, over the last century, the construction industry has continuously created efficiencies in manufactured products. So before designing an efficient home, start by utilizing efficiencies already used in the building industry. Plywood, or oriented strand board (OSB) sheets, and drywall board come in 4-foot widths. And building codes require wall framing wood studs spaced either every 16 or 24 inches apart. Therefore, it makes sense to utilize the 4-foot module when laying out the home’s footprint and individual room sizes. (More on this later.)
Design efficiency also begins at the macro level with the home’s shape. This was understood in the late 1900s with the emergence of the American Foursquare Farmhouse design (see Exhibit 1)—a square-shaped home that simplified construction through efficient design.
Exhibit 1: Foursquare Farmhouse Design

The square in Foursquare says it all: We’ve known since the Greeks that a square is more efficient than a rectangle. A great example is Euclid’s proof of Pythagoras’ Theorem (see Exhibit 2). A 20’x20’ shape has the same square footage as a 10’x40’ shape, but the 10’x40’ shape has 25% more linear wall space (100’ vs 80’). The closer the overall home’s shape is to a square, the more efficient it will be with material usage. As discussed, the 4-foot module width maximizes product usage while reducing waste. Therefore, use this module to lay out interior room sizes, exterior window locations and overall perimeter distance to efficiently maximize material usage.
Exhibit 2: Euclid’s Proof of Pythagoras’ Theorem
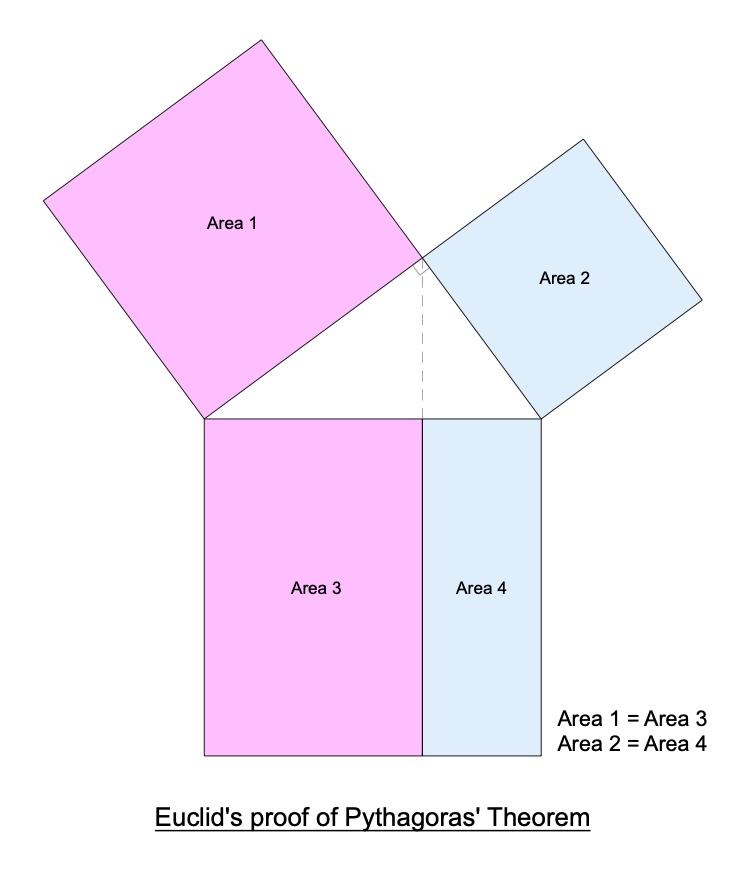
In addition to the home’s shape and the 4-foot module, circulation is another contributor to design efficiency. Office high-rise towers are designed with a core, which contains the vertical circulation system and the primary structural and mechanical systems. This central location provides maximum floor-plate efficiency (leasable space), which historically has been around 75%-80%, or 20%-25% for the core and exterior building envelope (wall).
While this metric doesn’t translate directly to residential homes, the concept of centralized circulation does. Homes, like office towers, are most efficient when circulation is centralized to maximize useable space. When designing an efficient home, centrally locate a u-shaped stair on the longitudinal axis. The u-shape allows the stair’s landings to be located internally, away from the exterior wall at the interior hallway or horizontal circulation. This reduces a hallway’s distance to a few feet on each floor from the stairs and increases floor-plate efficiency. An achievable floor plate for a residential home is around 80%, or 20% for stairs, hallway and exterior walls.
A centralized circulation scheme is enhanced by a multi-story home. A two-story home with a basement (location dependent) is best, but an attic level can easily be accomplished with an appropriate roof design.
Good design doesn’t require complicated solutions, just solutions that utilize efficiencies and guidelines already used in the construction industry. To illustrate these guidelines, I’ve created a simple house design based on a 4-foot grid that is slightly rectangular with centralized circulation. The layout utilizes common room types and sizes used by Hoffmans Architecture when designing custom homes. The design example and additional information on an efficient home design can be found in our Home Building Resource page.
Design Example
The aim of this design example is illustrating how an efficient home design can result in a market-based product that meets the contemporary homeowner’s needs. (Author’s note: The example illustrates a detached garage scheme. An attached garage scheme can be accomplished by locating the garage adjacent to the kitchen with a slight rearranging of the pantry and mud room to accommodate garage access.)
As discussed, a square house is the most efficient shape, but it’s very unlikely the overall house shape will be square. Therefore, a rectangular floor plate is likeliest to produce a useable house plan. As illustrated here, a slightly rectangular shape is easily attainable. Keep in mind, the closer it is to square, the more efficient it will be to construct. And be aware a large, square, single-story house is not efficient because it increases the concrete foundation and exterior wall linear footage. Therefore, to be efficient, a house must be two stories.
The challenge with any multi-story structure is locating the vertical circulation. Design efficiency is maximized by centrally located stairs, which is best accomplished via a u-shaped stair that locates the landing inward, adjacent to hallways and horizontal circulation. For most residential structures, a u-shaped stair is 10- to 12-feet long (stair run plus midway landing), which is a similar width to most bedrooms, kitchens, and dining rooms. Similarly sized rooms are easily arranged together for greater efficiency. The example shows the kitchen adjacent to the stairs, but the dining room could be located there, too, for an alternative layout.
The u-shape also opens up the possibility of an attic level without unnecessary roof-framing complexities and cost. A roof constructed with prefabricated roof attic trusses provides interior space without dormers or other secondary roof elements. The example assumes an attic truss with a 12/12 pitch that generates enough code-compliant headroom at the stair landing and attic level.
Good design requires discipline but also understanding constraints. Using the 4-grid module as a guide will help maintain design discipline while fostering critical constraints that will help produce an efficient design to minimize construction costs.
The example design is a PDF file located under the Additional Download section of the Home Building Resources page.
Design Example Data:
Size: 32’ x 36’
Square Foot Size:
Main Level: 1,133 SQ FT
Upper Level: 1,152 SQ FT
Total: 2,285 SQ FT
Attic Level: 623 SQ FT
Total w/Attic: 2,908 SQ FT